Technical Details
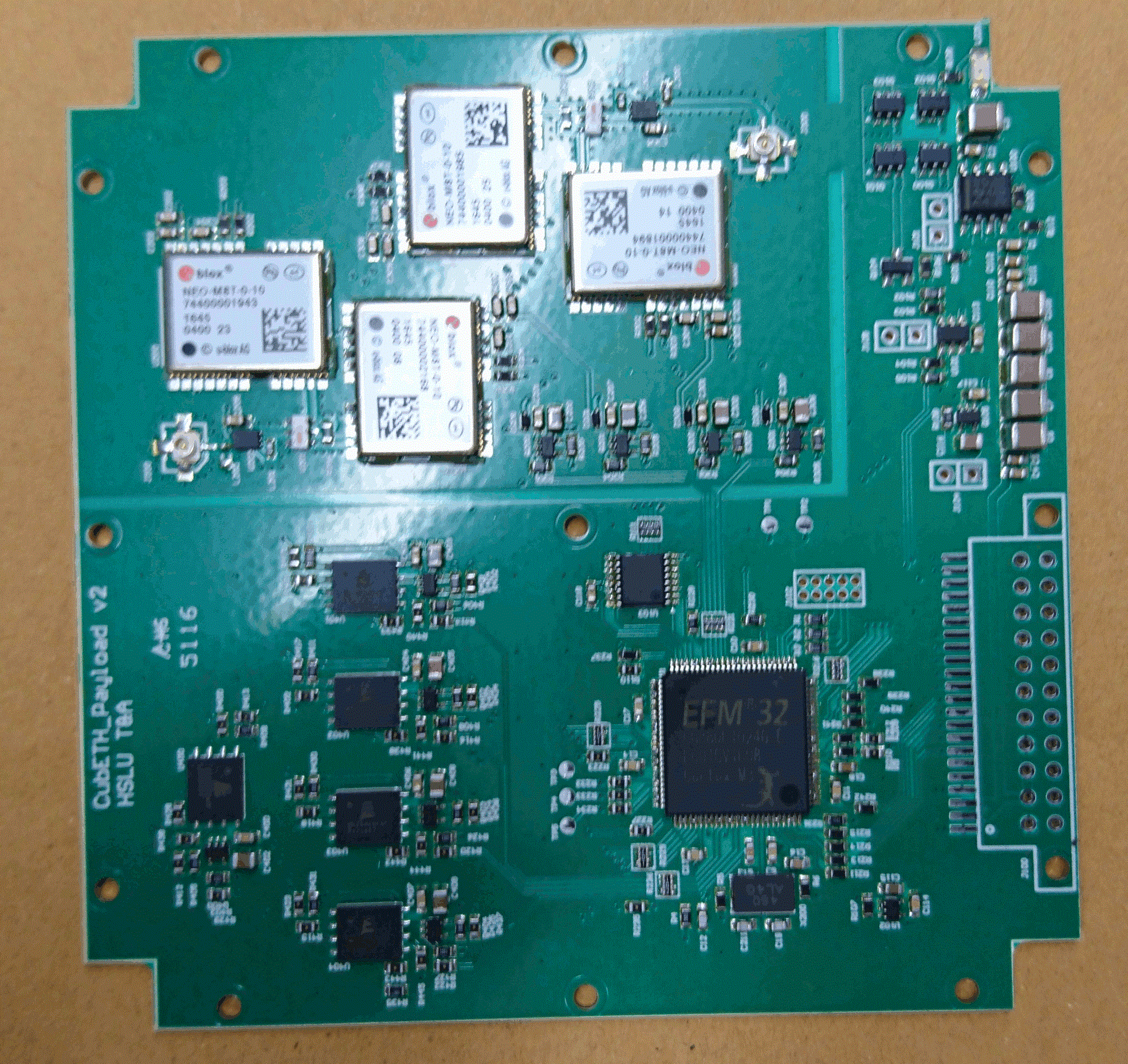
The main task of the GNSS payload board is to continuously provide the postition, velocity and accurate timing information to the satellite. This on-board PVT solution (Position, Velocity, Time) is computed by the receivers and is in the range of a few meters precision and about a micro second for timing. The communication to the satellite is based on an SPI interface, the communication of the board components is based on I2C.
The payload board comprises three main components.
GNSS receivers
Four commercial GNSS receivers are wired to the board. The receivers are mass market components produced by the Swiss company external page ublox. The chips are real multi-GNSS receivers, i.e., they are capable of tracking signals from all major satellite navigation systems (GPS, GLONASS, BeiDou, Galileo, QZSS). They are light-weight, cheap and operate on very low power. The positioning accuracy is a few meters.
As the receivers are not built for the extreme space environment, we included four of them for redundancy reasons. Should one fail, the next seamlessly kicks in.
Microcontroller
A powerful ARM microcontroller runs the payload firmware. The software is responsible for collecting and providing houskeeping data (temperature, status of the components, etc), scheduling the measurement scenarios, switching between different receivers in case of failures, and for communication with the satellite command module. The micro controller runs a real-time operating system (FreeRTOS) and is powerful enough to do some heavy computations. In a future firmware version an on-board real time solution is foreseen.
Memory
The board is equipped with 2.5 MB MRAM on-board memory for data storage. The files can be transferred to the satellite for downlink.
Space environmental testing
As none of the components (especially not the GNSS receivers) are space certified, our group put them to extensive environmental test during the development process. The GNSS receivers have been irradiated with a proton beam and put to vacuum under extreme temperature variations. Moreover, firmware stress tests are carried out ongoingly.